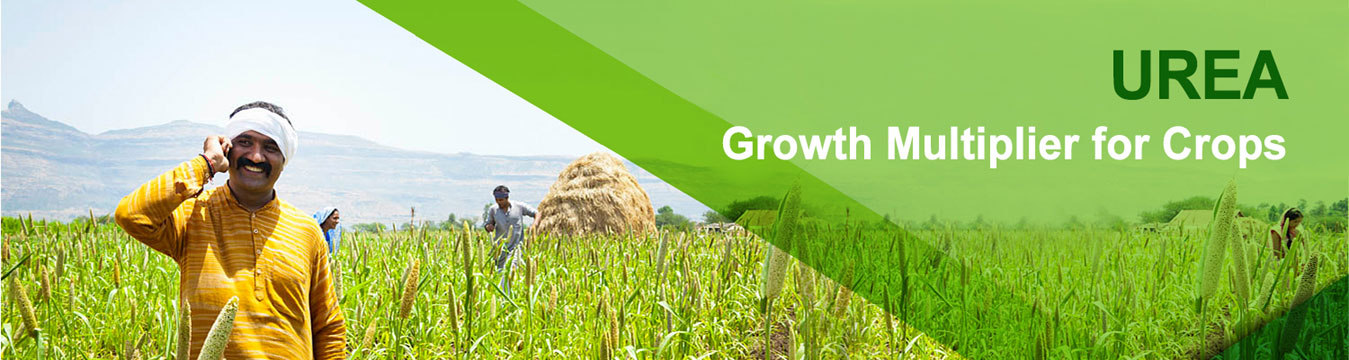
Urea
About Urea
Urea is a highly concentrated, solid, nitrogenous fertilizer, containing 46.0% Nitrogen. It is completely soluble in water hence Nitrogen is easily available to crops.
It contains Nitrogen in a milder form which changes to ammonical forms and is retrieved by soil colloids for longer duration. Urea is available in granular form and can be applied by drill and broadcasting.
Urea is ideally suitable for all types of crops and for foliar spray which instantly removes nitrogen deficiency. Urea also has a strong and long lasting effect on crop resulting in bumper crops. Carbonic acid present in Urea helps in absorption of other nutrients like phosphate and Potash by roots of crop.
Urea Manufacturing Process in RFCL
As part of Government of India initiative to revive the erstwhile Ramagundam Fertilizer complex located at Telangana, owned originally by M/s Fertilizer Corporation of India Limited (FCIL), a joint Venture Company under the name of Ramagundam Fertilizers and Chemicals Limited(RFCL),comprising M/s Fertilizer Corporation of India Limited (FCIL), M/s National Fertilizers Limited (NFL) and M/s Engineers India Limited (EIL) has been formed. RFCL has entrusted EIL to provide EPCM services for this complex. The RFCL complex is designed to have 3850MTPD single stream Urea Plant. For this Natural Gas is the main raw material. Reforming of Natural Gas with Steam and Air by catalytic reactions and other reactions at various subsequent steps produces Synthesis Gas and CO2. Synthesis Gas, a mixture of Nitrogen and Hydrogen gas is converted in to Ammonia in presence of another catalyst. Ammonia and CO2 gas further reacts in urea reactor and subsequent decomposition and concentration of the product obtained from urea reactor transforms into urea. The design capacity of ammonia Plant is 2200 MTPD and Urea Plant is 3850MTPD. Apart from Natural Gas and Air, Water and Electricity are also used in the process of making Urea. Associated utilities such as Water treatment, Effluent Treatment, Steam and Power Generation (in GTG-HRSG-UB), offsite facilities,Bagging and Railways Siding are also required for it. Distributed Control System (DCS) is the process instrumentation control to facilitate these chemical process and unit operations.Haldor Topsoe-Denmark and SAIPEM-Italy are the Process Licensor for Ammonia and Urea Plants respectively.
The process steps necessary for production of 3850MTPD Urea (SAIPEM as Process Licensor) are as under:
1) This section contains a technical description of urea plant with a nominal capacity to allow the production of 3850 MTPD of prilled urea. Snamprogetti ammonia stripping process is characterised by urea synthesis loop with an ammonia to carbon dioxide molar ratio at urea reactor inlet of 3.3 ~ 3.6. This allows a CO2 conversion into urea of 60 ~ 63 % in the reactor itself. Downstream the urea synthesis, the decomposition (and relevant recovery) of unconverted chemical reagents is carried out in three subsequent steps: i) High Pressure Decomposition in H.P. Stripper, ii) Medium Pressure Decomposition in M.P. Decomposer and,finally, iii) Low Pressure Decomposition in L.P. Decomposer.
2)The urea reactor effluent solution enters the stripper, under slightly lower pressure than the urea reactor, where a fair part of the unconverted carbamate is decomposed, with the help of the stripping action of excess NH3, so that the overall yield of the H.P. synthesis loop referred to CO2 is as high as 83~85% (on molar basis).
3) Downstream of the stripper residual carbamate and ammonia are recovered in two recycle stages namely Medium Pressure section and Low Pressure section respectively.
4) Ammonia and carbon dioxide vapours from the stripper top, after mixing with the carbamate recycle solution from M.P. section, are condensed, at the same pressure level of the stripper itself, in the H.P. carbamate condensers. After separating the inert gases which are passed to M.P. section, the carbamate solution is finally recycled to the reactor bottom by means of a liquid/liquid ejector, which exploits H.P. ammonia feed to reactors as motive fluid.
5) This ejector and the kettle-type carbamate condensers allow a horizontal layout, which is one of the main features of Snamprogetti process.
6) As it is necessary, in order to produce prill urea, to concentrate the urea solution up to 99.75% by wt., two vacuum concentration stages are provided. The solution leaving the low-pressure decomposer bottom with about 70% wt. urea is sent to the tube side of vacuum pre-concentrator where urea solution is concentrated. Urea solution is further concentrated in 1st and 2nd Vacuum concentrators up to 99.75%. The molten urea leaving the 2nd vacuum concentrator is sent to the prilling bucket by means of centrifugal urea melt pumps.
7) Droplets of molten urea from the prilling bucket fall along the natural draught prilling tower and solidify and cool while encountering a counter-current air flow.
8) Solid prills are collected at the centre of prilling tower bottom by means of the conical double arm rotary scraper, and through a conical hopper, they fall on prilling tower belt conveyor.The urea product is sent to the Bulk flow cooler package by product belt conveyor.
9) The final urea product is bagged in 45kg bags using semi-automatic machines and dispatched to farmer through Road/Rail routes.